
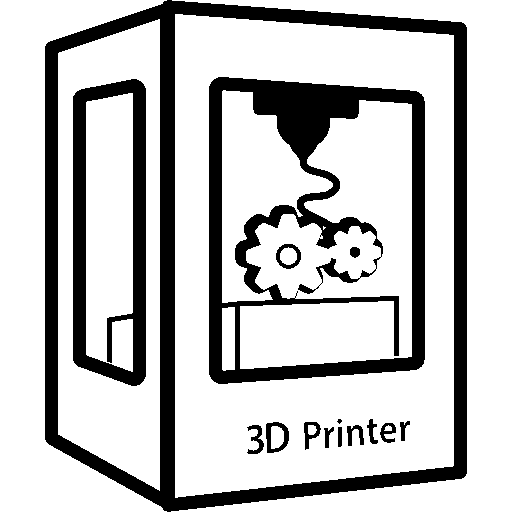
I’d go prusa mini at this price point. It’s a really reliable little machine, and easier to build than the MK3 and others. Enders are really not worth your time, trust me, I had one.
I’d go prusa mini at this price point. It’s a really reliable little machine, and easier to build than the MK3 and others. Enders are really not worth your time, trust me, I had one.
What things are you testing? If it’s really nothing to do with the way it looks cosmetically, then you will be fine with FDM. But for mockups for reviewers, you may want to just order them SLA’d from JLCPCB. I got a part made by them and the quality was phenomenal and it was super cheap and fast. It’s slower than printing it yourself, but the quality is worlds better and you would have to order hundreds and hundreds before it costs more than buying a printer.
For figures, and especially testing things that will compare to injection molding, going FDM is a really bad idea. It’s superior for engineering parts and rapid prototyping in basically all cases, but is has terrible dimensional accuracy by comparison, and it has a ton of trouble with thin features and overhanging shapes. This is mainly because the nozzle width is orders of magnitude wider than the pixels on a resin printer, so the slicer has to get very creative with dimensions to make complex models work at all. I am a huge FDM enthusiast, but this really isn’t the right place for it.
I’m a heavy parametric CAD user, so I’m not very knowledgeable on blender, but I do know a lot of people who use it for this sort of modeling. It does actually have some really good parametric CAD plugins for when you need mesh parts to work well with precise dimensions.
This can be caused by gantry misalignment/warping, or not registering the bed mesh properly. Also, maybe the bed is warped in some way that was in the middle of the test points, so maybe a finer mesh could fix this.
One thing about the bottom edge fillets, they actually can work for small radii. More than 1.5mm will start to show issues, but because of how small curves slice, it actually works below this value.
I just bought a bigger printer. No more seams! Realistically though, plastic welding or epoxy and paint, and a whole lot of sanding.
I have a very new Thinkpad (X1 extreme Gen 5) and it has been a lot of trouble. Started out with a bad battery which I had to get support to change out. A few months later one of the fans jammed, and instead of being replaceable like on older models, it was welded to the Mainboard, meaning that the entire board needed to be replaced, CPU GPU and all. A few months later, my performance took a huge hit, and I needed to get the Mainboard replaced yet again. The customer support was really great, but they definitely don’t build them like they used to.
They definitely just don’t know how to use mate connectors. I don’t prefer fusion over other CAD, but it’s not that fundamentally flawed as you say.
After switching to onshape, I have had the true revelation that it was actually solidworks fault the whole time for doing multibody modelling in a bad way.
Sounds like you’ll just end up with an ender 6. Maybe you can use that firmware and parts list and build guide?